Home » Three Phase Converter » 400v 50Hz equipment on 480v 60Hz power system
400v 50Hz equipment on 480v 60Hz power system
I set 400v 50 Hz three phase motor-driven equipment to run on 60 Hz systems many times per year, using variable frequency drives capable of full motor regulation. Use a 20% factor across the board in the programming.
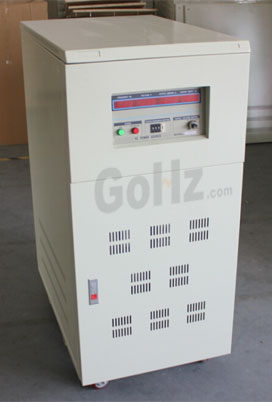
For example, an induction motor at 0.75 kW (approx. 1 HP), 50 Hz, 400v AC, set the motor Hz in the VFD to 60, then the Motor Voltage to 480v AC. This will increase the motor output to approx. 0.9 kW, (approx. 1.2 HP) with a corresponding increase in torque. Setting the motor speed (RPM) using the 20% factor is also essential. For example, if the motor speed @ 50 Hz is 1,400 RPM, dividing the RPM total by 0.8, results in a quotient of 1,750 RPM. By affording this balance of the Volts/Hz/RPM ratio, the equipment design criteria is very closely matched in the conversion.
In the US, the power grid is not as uniform as it is in many areas of Europe and elsewhere, with voltage levels fluctuating significantly from grid to grid. These levels will vary from approx. 460 VAC to 490 VAC in most areas in Wye Delta supply. In Grounded Delta (aka 'B' Phase Delta) the line variances can spread from 440 VAC to 525 VAC, depending on the power grid source and how many facilities draw power simultaneously along that grid supply.
As far as motor types from various manufacturers and how they respond, those I generally work with are ABB, Siemens, as well as several others sometimes private labeled for the equipment manufacturer using a variety of motors on their product lines. As the principle industries I'm involved in are overhead hoist & crane, conveyors, vacuum and pumping systems, all of the applications are constant torque, requiring a high starting torque capability. The only time issues may arise generally involves 400 VAC/50Hz/2,880 RPM/480 VAC/60Hz/3600 RPM motors, wherein some added applicable programming in a VFD is required to generate the necessary torque at start. Again, any VFD to be used must have the necessary capabilities of full motor regulation to effect the changes mentioned, and control the V/Hz output levels or motor damage can occur within a short time span of operation.
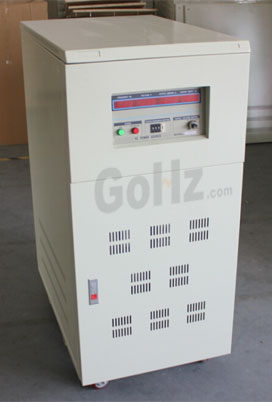
For example, an induction motor at 0.75 kW (approx. 1 HP), 50 Hz, 400v AC, set the motor Hz in the VFD to 60, then the Motor Voltage to 480v AC. This will increase the motor output to approx. 0.9 kW, (approx. 1.2 HP) with a corresponding increase in torque. Setting the motor speed (RPM) using the 20% factor is also essential. For example, if the motor speed @ 50 Hz is 1,400 RPM, dividing the RPM total by 0.8, results in a quotient of 1,750 RPM. By affording this balance of the Volts/Hz/RPM ratio, the equipment design criteria is very closely matched in the conversion.
In the US, the power grid is not as uniform as it is in many areas of Europe and elsewhere, with voltage levels fluctuating significantly from grid to grid. These levels will vary from approx. 460 VAC to 490 VAC in most areas in Wye Delta supply. In Grounded Delta (aka 'B' Phase Delta) the line variances can spread from 440 VAC to 525 VAC, depending on the power grid source and how many facilities draw power simultaneously along that grid supply.
As far as motor types from various manufacturers and how they respond, those I generally work with are ABB, Siemens, as well as several others sometimes private labeled for the equipment manufacturer using a variety of motors on their product lines. As the principle industries I'm involved in are overhead hoist & crane, conveyors, vacuum and pumping systems, all of the applications are constant torque, requiring a high starting torque capability. The only time issues may arise generally involves 400 VAC/50Hz/2,880 RPM/480 VAC/60Hz/3600 RPM motors, wherein some added applicable programming in a VFD is required to generate the necessary torque at start. Again, any VFD to be used must have the necessary capabilities of full motor regulation to effect the changes mentioned, and control the V/Hz output levels or motor damage can occur within a short time span of operation.
Post a Comment:
You may also like:
50Hz 60Hz Frequency Converter Setting
Using GoHz frequency converter to
Or customize your own converters.
- Convert 220v 50Hz to 110v 60Hz,
- Convert 120v 60Hz to 230v 50Hz,
- Convert 110v 60Hz to 240v 50Hz,
- Convert 480v 60Hz to 380v 50Hz,
- Convert 400v 50Hz to 460v 60Hz,
- Convert 240v 60Hz to 380v 50Hz,
Or customize your own converters.
Featured Articles
460v 60Hz motor on 400v 50Hz power ...
Often the European motors at 1hp size are universal for 50Hz or 60Hz power supply, as long as you have 400V x 50Hz and 460V x ...
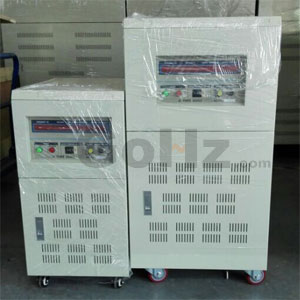
Convert 220v, 230v, 240v 50Hz to 110v, ...
When you buy an 110v (120v) 60Hz appliance from USA, and run it on 220v (230v, 240v) 50Hz country (i.e. UK, Australia, ...
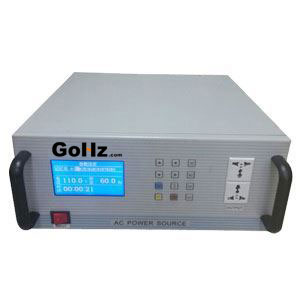
60Hz motor running on 50Hz power ...
Electric motors, both single and three phase, are designed for running on a specified power frequency. But sometimes we may use a ...
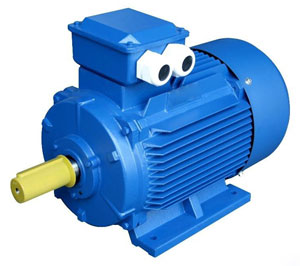
The European voltages are now standardized on 230V single-phase / 400V 3-phase. So that is the only Input choice available. Unlike the American systems where there there are still a wide range of different standards.